OVERVIEW
Building value in air – from the beginning.
Greenheck has come a long way since 1947 when it began business as a tiny sheet metal shop in Schofield, Wisconsin. Founders Bob and Bernie Greenheck promoted a business philosophy based on two main concepts — continuous improvement and the determination to be the easiest company to do business with. That approach drove the company's growth to become a global leader in the air movement, control, and conditioning industry. Bob and Bernie’s philosophy is captured in our motto “building value in air”… it’s our commitment to our customers and it remains the fundamental driving force behind our company’s mission and success.
Today, Greenheck fans, energy-recovery ventilators, packaged ventilation, make-up air units, dampers, louvers, kitchen ventilation systems, laboratory exhaust systems, and coils are shipped around the globe. You will find our flagship ventilation products behind walls, in ductwork, and on the roofs of hospitals, office buildings, hotels, shopping malls, restaurants, schools, industrial plants, warehouses, data centers and other commercial buildings. The function of each is to move air in, out and around a building — making life inside a lot more pleasant.
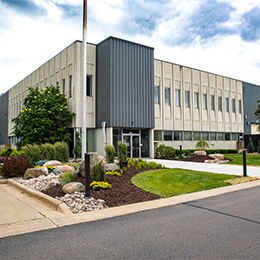
Vision, Purpose & Values
- Easy to do business with
- Ongoing investments in people and operations
- Making a difference in the community
- Mutually beneficial partnerships with sales partners and suppliers
- Integrity and professionalism
- Continuous improvement through learning, innovation, and teamwork
Ìý
Investing in Itself
Leading in Innovation

Robert C. Greenheck Innovation Center
Greenheck’s own development and testing facilities at the U.S. Headquarters are acknowledged as the industry’s best. Here, new designs are explored, placed through comprehensive and demanding evaluation procedures and rated for specific performance requirements.
Our dedication and commitment to creating and building innovative solutions is constant and evolving. We opened the doors of a new 72,000 square foot state-of-the-art research and testing facility named the Robert C. Greenheck Innovation Center in late 2015. The facility uses sound, airflow measurement and psychrometric labs, product prototyping, and dedicated space to develop and fine-tune manufacturing processes. It also includes office space to support our technical employee growth and foster an environment for collaboration and innovation.
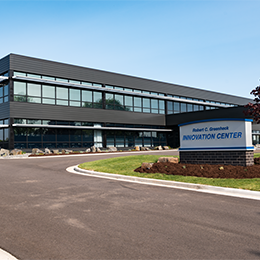
Manufacturing Leadership
Greenheck continually looks for ways to improve and innovate throughout the company. Improving operational efficiencies has been a critical factor to our success. It is driven by a corporate strategy to achieve Operational Excellence.
Year-over-year productivity improvement has enabled Greenheck to offset the impact of increasing costs and still provide competitively priced products to our customers. This in turn has allowed the business to grow and to capture increased market share.
Great strides have been made toward our Vision of Operational Excellence through:
- Sustaining our continuous improvement initiative, the Greenheck Performance System (GPS).
- Investing capital aggressively back into the business providing state-of-the-art manufacturing technology and tooling.
- Partnering with suppliers to optimize value throughout the entire supply chain.
Through these strategies, Greenheck is blending best manufacturing practices to create flexible, low-cost processes that provide unmatched value to our customers. Greenheck's Vision of Operational Excellence consists of a well-trained workforce, easily visualized systems and cost-effective equipment focused on value-added operations.
Value Engineering - Assuring Suppliers’ Processes Deliver Maximum Value
We have applied many significant process improvements over the past few years. At Greenheck, continuous improvement is a journey, not a destination.
Greenheck Performance System - A Continuous Improvement Initiative
In May 2002, the Greenheck Performance System (GPS) was launched. Through this initiative, employees have been educated and have implemented the proven methodologies of Design for Excellence, Maintenance Excellence, and Lean Manufacturing throughout the entire organization. Each of these methodologies directly correlates to the manufacturing processes employed.
For example, through Design for Excellence Strategies, Greenheck challenges itself to deliver maximum value to customers through our product designs. This product design strategy uses cross-functional teams to exploit manufacturing processes and creativity. Our Maintenance Excellence Strategy strives for optimal equipment repeatability and availability. The equipment employed must be dependable and capable, especially as inventories are reduced and move closer to just-in-time production with single-piece flow. Through Lean strategies, we focus on maximizing the value in each value stream eliminating waste and non-value added activities.
Bernard A. Greenheck Education Center
The Bernard A. Greenheck Education Center features Greenheck air movement, conditioning and control products. This facility on the Schofield campus offers a tremendous learning experience for visiting
- Mechanical engineers
- Contractors
- Architects
- Manufacturer’s reps
The center offers visitors information on product features and applications. Learning is heightened with the use of simulated and virtual installations along with working product displays. There are several meeting rooms and a main presentation room complete with full multimedia capabilities. It is an ideal training site for thousands each year.
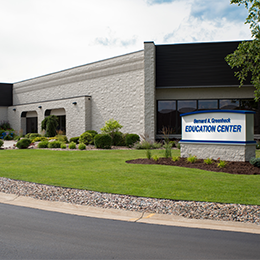